Description:
Discover the power of What is Parametric 3D Modeling, a method that brings flexibility, accuracy, and efficiency to modern design. This in-depth guide explores how parametric modeling works, its benefits, and why it’s transforming industries like architecture, engineering, and product development.
Introduction
In the world of 3D design and engineering, innovation doesn’t just come from creativity—it also stems from efficiency and adaptability. What is Parametric 3D Modeling is a game-changing approach that combines mathematical logic with creative design, enabling designers and engineers to create highly flexible and modifiable digital models. Unlike traditional modeling, which can be rigid and time-consuming to edit, parametric modeling allows for dynamic changes driven by parameters such as dimensions, constraints, and formulas.
As industries increasingly rely on digital design tools to streamline workflows, parametric modeling is becoming an essential skill for professionals working in architecture, mechanical engineering, industrial design, and product development. In this blog, we’ll explore What is Parametric 3D Modeling is, how it works, its advantages, real-world applications, and why it’s such a powerful method in modern design.
What is Parametric 3D Modeling?
What is Parametric 3D Modeling is a type of modeling where geometry is created and controlled using parameters—defined variables such as length, height, radius, thickness, or even formulas. These parameters can be adjusted at any time, and the model updates accordingly.
In simpler terms, parametric modeling is like giving your design a brain. Instead of manually changing shapes every time you need to tweak a part, you set up relationships and rules so the model adapts on its own.
For example, if you design a table with a height of 75 cm and later decide to change it to 90 cm, you only need to update the height parameter—and the entire table adjusts itself automatically, maintaining proportions and other defined relationships.
How What is Parametric 3D Modeling
At the core of parametric modeling are parameters and constraints:
- Parameters: These are numerical values or expressions assigned to control dimensions, angles, and positions (e.g., “width = 50 mm”).
- Constraints: These define geometric relationships like parallelism, perpendicularity, symmetry, or tangency (e.g., “this edge must stay parallel to this other edge”).
These elements are built into the model using a history-based system, meaning the software keeps a record of every modeling step. If a parameter changes, the software recalculates all related steps, updating the model intelligently.
Software that supports parametric modeling includes:
- SolidWorks
- Autodesk Fusion 360
- PTC Creo
- Siemens NX
- FreeCAD
Each of these platforms allows designers to build smart, modifiable geometry that’s easy to reuse and adapt.
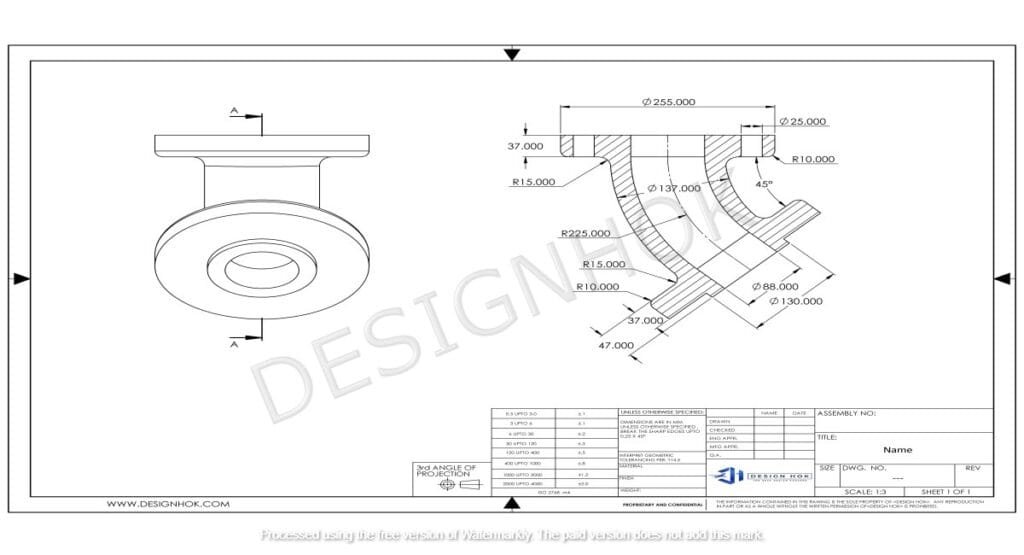
Key Benefits of What is Parametric 3D Modeling
1. Design Flexibility
With parameters controlling geometry, making design changes is quick and easy. This is especially helpful when clients request revisions or when testing different design iterations.
2. Efficiency in Workflow
Rather than rebuilding models from scratch, designers can update parameters to produce variations—saving hours of work.
3. Greater Accuracy
Constraints help eliminate errors. For example, setting two holes to always be the same distance apart ensures consistent spacing, even if the object’s size changes.
4. Easy Design Reuse
Once a parametric model is created, it can be reused in future projects by simply adjusting the input values, reducing the effort required to design from scratch.
5. Collaboration-Ready
Engineers and designers working in teams benefit from parametric models because they’re structured, understandable, and easy to modify without disrupting the entire design.
6. Ideal for Simulation and Testing
Many simulation tools are built on parametric systems, allowing for real-time testing of various design iterations under stress, load, or motion.
Real-World Applications of Parametric Modeling
1. Mechanical Engineering
In mechanical design, parametric modeling is used to build machine parts, assemblies, and enclosures. Engineers can adjust one part and automatically see the effects on the rest of the system, reducing errors and design conflicts.
2. Architecture and Construction
Architects use parametric design to model buildings, facades, and structures. By adjusting height, materials, or angles, they can quickly explore different configurations without redrawing everything.
3. Industrial Design
Product designers use parametric tools to create prototypes of consumer products. Whether it’s a bottle, chair, or tech gadget, every part of the product can be scaled and optimized using parameter-driven control.
4. Automotive and Aerospace
These industries rely on precision and adaptability. Parametric modeling helps design vehicle bodies, engine parts, and aircraft components, ensuring parts integrate seamlessly while allowing for changes.
5. Education and Research
Parametric modeling is increasingly used in research projects and academic design competitions, where quick iteration and real-time adaptability are key.
Parametric vs. Direct Modeling
To fully understand parametric modeling, it’s important to know how it differs from direct modeling.
Feature | Parametric Modeling | Direct Modeling |
---|---|---|
Design History | Yes, based on step-by-step operations | No, geometry is edited directly |
Flexibility | Highly flexible via parameters | Flexible, but less automated |
Best For | Complex, feature-driven designs | Simple or conceptual modeling |
Learning Curve | Steeper | Easier to start with |
Example Tools | SolidWorks, Fusion 360 | Blender, Rhino (without Grasshopper) |
While direct modeling is often used for artistic or early concept work, parametric modeling shines in technical and production-ready environments.
Challenges of Parametric Modeling
Despite its many advantages, parametric modeling has a few challenges:
- Steeper Learning Curve: Beginners may find it complex due to the logic-based approach.
- Over-Constraint Errors: If too many constraints or conflicting rules are applied, the model can become unstable or fail to update properly.
- Performance: Large parametric models can become slow as they recalculate every time a parameter changes.
However, with practice and good modeling habits, these challenges become manageable and well worth the effort.
Conclusion
What is Parametric 3D Modeling is not just a trend—it’s a cornerstone of modern digital design. By combining flexibility, accuracy, and intelligent control, parametric modeling empowers designers and engineers to create smarter, more efficient designs. Whether you’re building machines, consumer products, architectural forms, or complex systems, parametric tools help you adapt, innovate, and deliver higher-quality results.
For businesses like DesignHok, parametric modeling isn’t just a method—it’s a philosophy of working smarter, not harder. As technology evolves and client expectations grow, parametric modeling ensures your design process is always a step ahead.
FAQs: What is Parametric 3D Modeling?
Q1: Is parametric modeling only for engineers?
No. While engineers use it extensively, architects, product designers, and even artists benefit from parametric modeling because it offers control and flexibility.
Q2: What software is best for parametric modeling?
Popular choices include SolidWorks, Fusion 360, Siemens NX, and FreeCAD. Each offers parametric features suitable for different industries and levels of expertise.
Q3: Can I use parametric modeling for 3D printing?
Yes. Parametric models are perfect for 3D printing since you can easily change dimensions and export to STL files for slicing.
Q4: How is parametric modeling different from CAD?
Parametric modeling is a type of CAD (Computer-Aided Design). It focuses on models that are driven by parameters and constraints rather than just direct geometry editing.
Q5: Is parametric modeling difficult to learn?
It can be challenging at first, especially if you’re used to direct modeling. However, with consistent practice and tutorials, it becomes a highly rewarding skill.
Q6: What industries use parametric 3D modeling the most?
Engineering, architecture, automotive, aerospace, and product development all rely heavily on parametric modeling.