The oil and gas industry operates in one of the most demanding environments known to engineering. From extreme temperatures to high-pressure systems, the mechanical components used must be robust, reliable, and tailored to specific use cases. That’s where custom mechanical design for oil and gas projects becomes not just helpful—but absolutely essential.
In this article, we’ll explore why personalized engineering solutions are critical in the energy sector, the key components involved, and how custom designs can drive both safety and performance in field operations.
Why Mechanical Design for Oil and Gas Is Not One-Size-Fits-All
Off-the-shelf mechanical components may work for general industrial applications, but they often fall short in oil and gas environments. The harsh and often unpredictable nature of drilling, refining, and transporting hydrocarbons demands mechanical design for oil and gas that is custom-built to withstand both physical and chemical extremes.
When mechanical systems fail in oil fields or refineries, the consequences are significant—ranging from production downtime and environmental damage to human injury. A tailored design minimizes these risks and increases operational reliability.
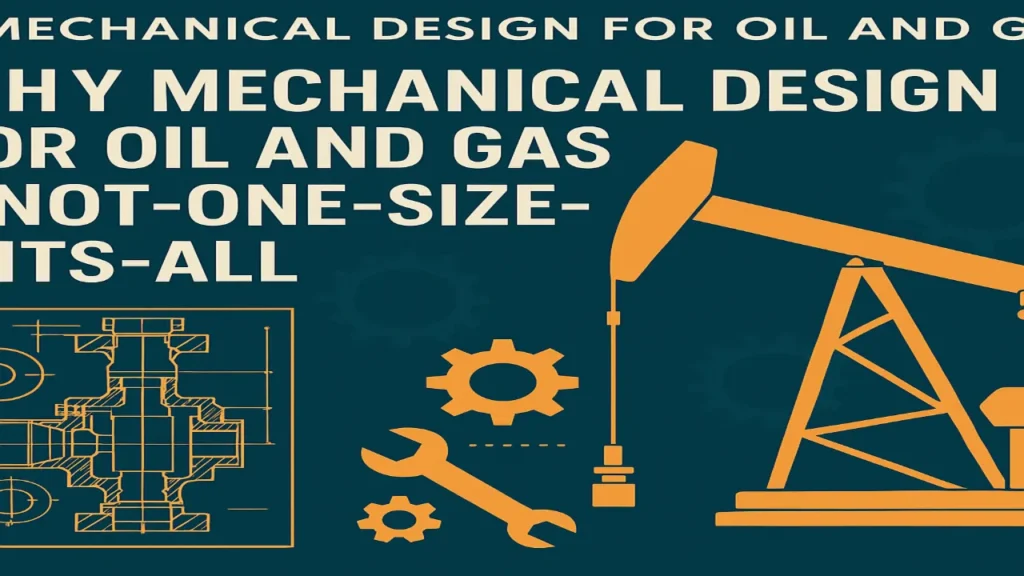
Critical Components in Custom Mechanical Design
1. Pressure Vessels and Tanks
These are core elements in almost every oil and gas plant. Whether you’re storing crude oil or separating gas from liquids, the internal pressure, temperature, and corrosive properties of contents demand specialized design calculations and material selection.
2. Piping Systems and Manifolds
Unlike standard pipelines, the mechanical design for oil and gas involves precise routing to reduce flow resistance, avoid vibration-induced fatigue, and ensure ease of maintenance.
3. Structural Supports and Brackets
Supporting heavy loads in seismic or offshore environments isn’t simple. Custom support systems are needed to anchor equipment effectively while allowing for expansion and contraction caused by heat.
4. Heat Exchangers and Cooling Systems
Thermal regulation is critical. Whether in desert oilfields or deep-sea rigs, your cooling system must be tuned specifically to the ambient and operational conditions.
7 Powerful Benefits of Custom Mechanical Design in Oil and Gas
1. Reduced Equipment Failure Rates
Custom design minimizes the risk of material fatigue, corrosion, or thermal breakdown. Equipment made specifically for oil and gas parameters is less likely to fail during critical operations.
2. Enhanced Safety Compliance
With stricter regulations from bodies like OSHA, ASME, and API, compliance is non-negotiable. A tailored mechanical design for oil and gas projects guarantees you stay ahead of audits and avoid fines.
3. Increased System Efficiency
When all components are designed to work in harmony, energy consumption drops, and process flow becomes optimized. You get more output with less input.
4. Flexibility for Complex Environments
Whether you’re operating in Arctic conditions or corrosive marine environments, a generic system won’t suffice. Custom mechanical design provides adaptive solutions based on site-specific challenges.
5. Better Lifecycle Cost Management
Initial investment in custom designs might seem higher, but the reduced need for repairs, replacements, and unplanned shutdowns results in long-term savings.
6. Easier Integration with Automation Systems
Modern oil and gas projects rely heavily on digital automation. A well-thought-out mechanical design for oil and gas ensures that physical systems are sensor-ready and easy to integrate with software platforms.
7. Competitive Edge in Bidding and Client Trust
Clients and stakeholders trust teams that engineer for reliability and excellence. Demonstrating your custom mechanical capabilities can give you a persuasive edge in competitive tenders.
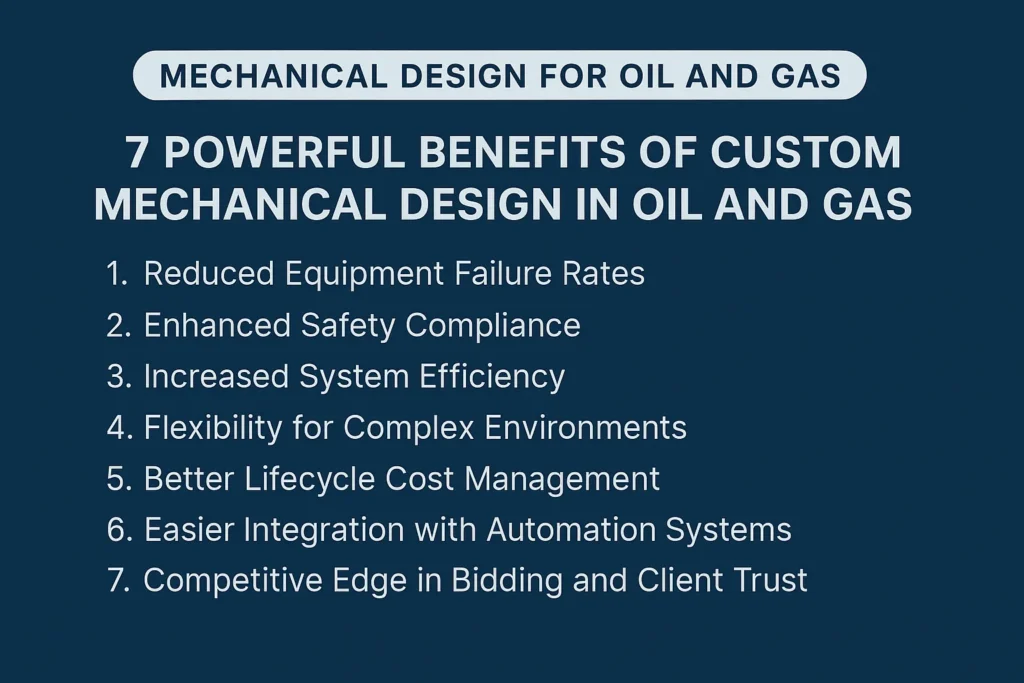
Key Challenges in Designing for Oil and Gas Projects
While the benefits are numerous, mechanical design in this sector also presents some major hurdles.
- Material Selection: Corrosive fluids, high pressure, and temperature fluctuations can limit your options. Exotic metals may be needed, which drive up costs.
- Logistics and Assembly: Custom systems must be designed for ease of transport and installation, especially in offshore or remote areas.
- Design Standardization vs. Customization: It’s a fine line—how do you balance the need for uniqueness with the economies of standard parts?
Solving these requires deep domain expertise and a commitment to lifecycle thinking from the design phase.
Case Example: Custom Piping Skid for a Middle East Refinery
A refinery in the Middle East needed a modular piping skid that could handle high sulfur content, extreme ambient heat, and rapid pressure fluctuations. Standard designs had failed due to gasket blowouts and thermal cracking.
Through custom mechanical design for oil and gas, the engineering team:
- Used Inconel 625 for high corrosion resistance
- Designed flexible bellows to absorb shock waves
- Installed remote monitoring sensors for predictive maintenance
The result? 22% increased uptime and a 30% reduction in maintenance costs within the first year.
XO: Smart Design Practices That Prevent Future Downtime
The future of mechanical design for oil and gas is intelligent, predictive, and proactive. Here are a few smart design practices that help:
- Digital Twin Modeling: Simulate the entire system before physical fabrication to detect failure points early.
- Redundancy in Design: Critical systems have backup mechanisms, from valves to drives, built into the design.
- Remote Maintenance Access: Design components so they can be inspected or replaced using drones or robotic tools.
This kind of proactive planning transforms reactive maintenance into predictive success.
Frequently Asked Questions (FAQ)
Q1: Why is custom mechanical design necessary in oil and gas projects?
Because off-the-shelf components often don’t withstand the extreme operating conditions of oil and gas applications, leading to failures, downtime, and safety risks.
Q2: How does custom design improve safety?
It ensures all components meet or exceed regulatory standards, are tested for extreme conditions, and integrate seamlessly with safety protocols.
Q3: What role do materials play in mechanical design for oil and gas?
Material selection is crucial—corrosion resistance, heat tolerance, and stress durability must all be considered to avoid early failure.
Q4: What is the ROI of custom mechanical design?
While upfront costs are higher, the long-term benefits—reduced failures, fewer shutdowns, and extended equipment life—offer substantial returns.
Q5: Can these designs be modified for different projects?
Yes. A well-structured design process uses modular thinking, making it easier to adapt core systems across different applications.
Final Thoughts: Why It’s Worth the Investment
In today’s volatile energy market, risk tolerance is low, and operational excellence is critical. Mechanical design for oil and gas is no longer an afterthought—it’s a strategic function. A poor design decision today can lead to millions in losses tomorrow.
With advanced mechanical design for oil and gas also in simulation, materials science, and predictive analytics, custom designs are more accessible than ever. By investing in customized mechanical solutions, companies secure not just efficiency but also a significant safety and reputational advantage.