Description:
Discover how Fusion 360 3D Modeling Guide for DesignHok to deliver accurate, professional, and efficient 3D modeling services. This guide walks you through the powerful features, workflow, and advantages of using Fusion 360 for mechanical and product design.
Introduction
In a fast-moving digital world, where precision, innovation, and collaboration define success, 3D modeling plays a vital role in shaping the future of design and engineering. Whether it’s product development, mechanical design, or prototyping, having a powerful modeling tool is essential. At DesignHok, Fusion 360 stands as our go-to 3D modeling software due to its versatility, accuracy, and integrated design-to-manufacture workflow.
Fusion 360 3D Modeling Guide for DesignHok platform developed by Autodesk. It’s a favorite among professionals because it brings together parametric modeling, sculpting, simulation, rendering, and collaboration all in one environment. This blog serves as a complete Fusion 360 3D modeling guide tailored to how DesignHok uses it to deliver high-quality models for clients across various industries.
Why DesignHok Uses Fusion 360
At DesignHok, delivering top-tier mechanical and product design solutions is at the heart of our work. Fusion 360 helps us streamline this process with:
- All-in-One Workspace – Design, engineering, simulation, and manufacturing in one tool.
- Cloud Collaboration – Real-time project sharing and feedback with team members and clients.
- Precision Tools – Advanced parametric modeling and simulation features.
- Cost Efficiency – Lower software costs with powerful results.
- Flexibility – Ideal for both industrial designs and complex mechanical systems.
Whether it’s for custom parts, assemblies, or prototypes, Fusion 360 allows us to bring ideas to life with unmatched accuracy and creativity.
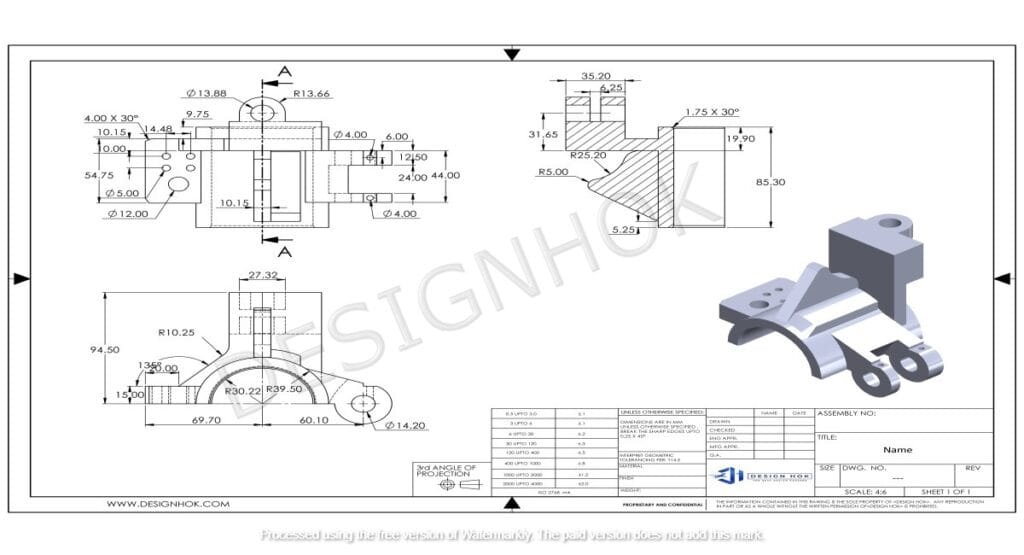
Step-by-Step Guide to Fusion 360 3D Modeling Guide for DesignHok
Let’s break down our typical 3D modeling process using Fusion 360:
Step 1: Starting a New Project
Once a new client project is initiated, we start by creating a new project folder in Fusion 360’s cloud environment. This allows all stakeholders to access and collaborate on the same files securely.
We gather all the initial details, such as
- Sketches or reference images
- Technical dimensions
- Material preferences
- Functional requirements
This helps our designers visualize what needs to be modeled.
Step 2: Sketching the Base Design
Using Fusion 360’s Sketch environment, we create 2D profiles as the foundation of the 3D model. These sketches are drawn on planes (XY, YZ, XZ) and include:
- Lines, circles, and arcs
- Dimensions and constraints
- Profiles for extrusion or revolving
These sketches are fully parametric, which means any dimensional change will automatically update the model. This is ideal for revision-heavy projects.
Step 3: Creating the Fusion 360 3D Modeling Guide for DesignHok
Once the sketch is ready, we move to the Solid Modeling workspace, where we transform 2D sketches into 3D bodies using
- Extrude—to pull 2D profiles into 3D solids
- Revolve—to rotate profiles around an axis for cylindrical shapes
- Loft—to create organic shapes between different profiles
- Sweep—for creating complex pipe-like or rail-based geometry
This is where the model takes shape. We apply fillets, chamfers, holes, and other modifications to meet design requirements.
Step 4: Assembling Multiple Parts
For projects with multiple components, we use the Assembly workspace to position parts using joints and motion constraints. Fusion 360 3D Modeling Guide for DesignHok allows dynamic simulation, helping us verify how parts interact—crucial in mechanical assemblies.
At DesignHok, we use this feature to model:
- Gear systems
- Hinges and mechanical joints
- Electronic enclosures
- Tool designs
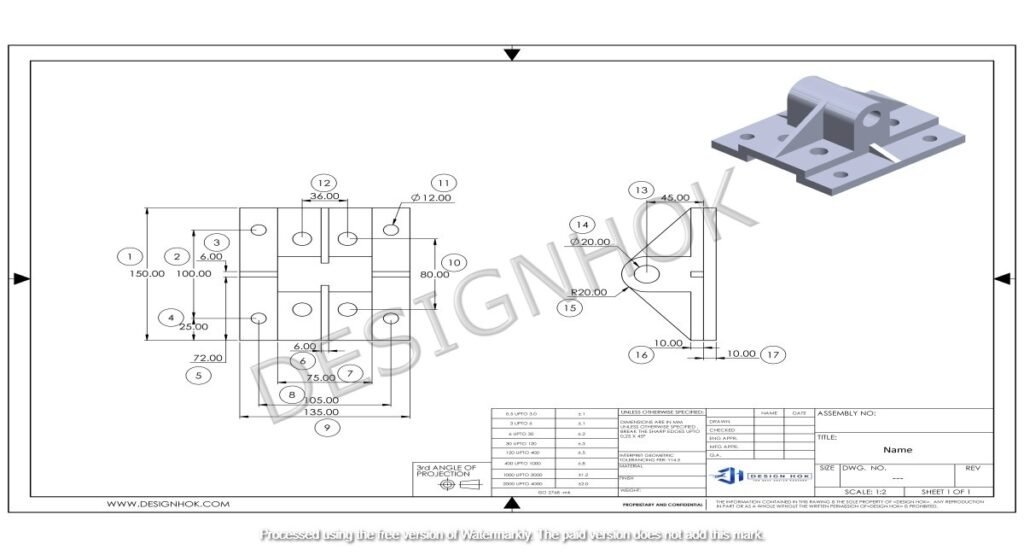
Step 5: Material Selection and Rendering
We apply materials and appearances to the model from Fusion 360’s built-in library or create custom ones. This step is essential for visualization.
Using the Render workspace, we generate high-quality images that are:
- Used for client presentations
- Shared in portfolios
- Added to project proposals
The rendering engine in Fusion 360 3D Modeling Guide for DesignHok supports real-world lighting and environment settings for realistic output.
Step 6: Simulation and Testing
Before finalizing the model, we often run simulations for stress analysis, thermal tests, or motion studies. This is especially useful for functional parts and mechanical components.
Fusion 360 3D Modeling Guide for DesignHok help ensure that the model performs well under real-world conditions, avoiding potential design failures.
Step 7: Exporting Files for Manufacturing or Sharing
We export the final model in various formats depending on the client’s needs:
- STL or OBJ for 3D printing
- STEP or IGES for CNC or CAD collaboration
- PDF or image renders for documentation
Fusion 360 allows seamless integration with manufacturing workflows, including CAM and 3D printing platforms.
Benefits of Fusion 360 3D Modeling Guide for DesignHok Clients
Here’s why our clients love that we use Fusion 360 for their 3D modeling projects:
- Faster Turnaround – Integrated tools speed up the entire design process.
- High Accuracy – Dimensional control and parametric edits ensure quality.
- Cost Savings – Early error detection reduces prototyping costs.
- Collaborative Access – Cloud sharing means real-time updates and client input.
- Realistic Visualization – Renders and simulations bring clarity before production.
Whether you’re developing a product prototype or designing machinery, Fusion 360 ensures every detail is addressed efficiently.
Applications at DesignHok
We use Fusion 360 3D Modeling Guide for DesignHok for a variety of design services, including:
- Mechanical Components Design
- Consumer Product Prototypes
- Industrial Tooling and Jigs
- Sheet Metal Design
- Plastic Mold Design
- 3D Printable Designs
Our ability to handle projects from concept through to manufacturing makes us a one-stop solution for product development.
Conclusion
Fusion 360 3D Modeling Guide for DesignHok—it’s an all-in-one design solution that supports every phase of the product development journey. At DesignHok, we harness its power to deliver innovative, high-quality, and efficient design services to clients worldwide.
From ideation to presentation and even simulation, Fusion 360 enables us to handle projects with confidence and creativity. So if you’re looking for a reliable partner who uses cutting-edge tools to transform your ideas into tangible designs, DesignHok and Fusion 360 are the perfect match.
FAQs: Fusion 360 3D Modeling Guide for DesignHok
Q1: What is Fusion 360 used for at DesignHok?
A: We use it for 3D modeling, mechanical part design, product development, simulation, rendering, and manufacturing-ready file preparation.
Q2: Can you modify my existing Fusion 360 files?
A: Yes, we can review, edit, and improve existing Fusion 360 projects to meet your updated requirements.
Q3: What industries do you serve using Fusion 360?
A: We work with clients in mechanical engineering, product design, consumer goods, industrial tooling, and 3D printing.
Q4: Do I need to have Fusion 360 to view the models?
A: No. We can share files via web links, images, or video walkthroughs. Clients without Fusion 360 can still review visuals easily.
Q5: How long does it take to complete a 3D model?
A: Timelines depend on project complexity. Simple parts can be done in 1–2 days, while complex assemblies may take a week or more.
Q6: Can you prepare models for 3D printing or CNC machining?
A: Absolutely. We export models in STL, STEP, or IGES formats with the correct tolerances and guidelines for manufacturing.
Q7: Is Fusion 360 better than other modeling tools?
A: It depends on the use case. Fusion 360 is excellent for mechanical and product design due to its integrated features, cloud collaboration, and ease of use.